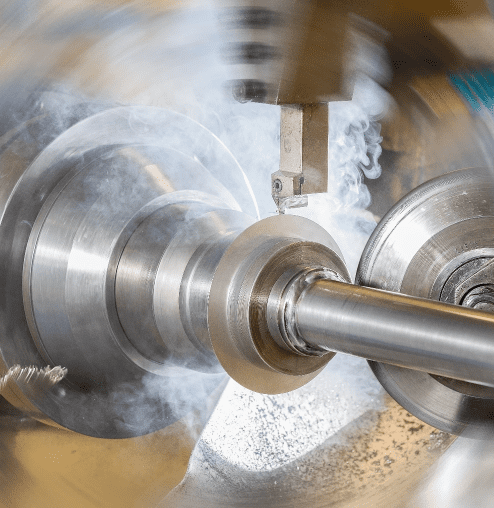
Guide
WHAT IS METAL SPINNING?
Metal spinning, also known as spin forming, is a metalworking process where a disc of metal is rotated at high speeds and formed into an axially-symmetric part using spin tools. Picture the art of pottery sculpting, but envision it in a horizontal plane, and instead of molding clay, we’re shaping metal! Metal spinning is used in various industries to produce a wide range of products—anything from architectural pieces, speciality lighting, and decorative household goods to cookware, gas cylinders, and much more. For cones and domes, specifically, the roller tool exerts force onto the sheet metal while spinning, pushing the metal onto the mandrel and creating a seamless, symmetrical, and smooth product. This manufacturing process is particularly effective for creating rounded or conical shapes.
What Raw Materials Can Be Used?
Typically, the most common types of metals that are being spun in our shop are aluminum, stainless steel, and mild steel. Without getting into the deep specifics, different metals have different properties, so the preferred metal for cones and domes depends on the application of the part. Mild steel tends to be more cost-effective, but it is prone to rust under certain weather conditions. Aluminum won’t rust, but it is a much softer metal when compared with stainless steel.
WHAT PRODUCTS CAN BE MADE?
There are many examples of products that are made from conical and dome-shaped metal spinning, some of which many of us see and walk past every day. Here are some examples:
What Sizes Can Be Achieved?
This group about cylindrical and ring-like shapes have almost identical spinning capabilities as the first group about the conical and dome shapes. Of course, the shapes and geometries are different, but the biggest OD being spun and material thickness limitations are the same as the conical and dome-shaped sections. Our maximum blank diameter for spinning is still 102”.
Instead of repeating the capabilities, here are some differences:
Cone/Funnel/Bell-Shape Capabilities
The outside diameter of the cones can reach impressive sizes, typically ranging up to 50”, depending on the specific part.
The inside diameter of the cones and funnels we can metal spin is highly versatile, accommodating sizes as small as an inch.
For larger diameter cones, a rolling process is used, joined with a weld seam.
Dome/Hemisphere Capabilities
The domes boast a substantial outside diameter capability of up to 60”, limited by the material size availability rather than the machine.
A necessary inside diameter hole for the metal spinning tool is incorporated into the dome design—however, it can be conveniently plug welded in the different operation.
Thickness
Here’s a chart of KRYTON’s metal spinning material thickness capability:
Mild Steel |
⅜” (0.375”) |
Stainless Steel |
3/16” (0.1875”) or 7 Gauge |
Aluminum |
½” (0.5”) – Must Be O-Tempered |
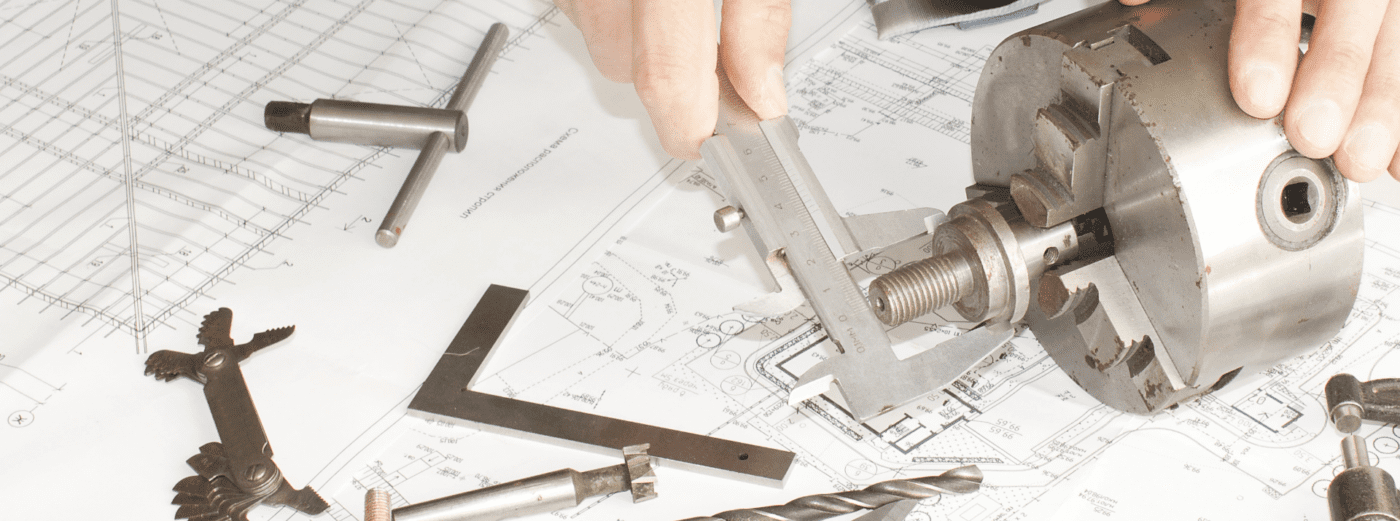
Kryton Metals
Quality Control
Our product quality control process is meticulous and thorough, ensuring the highest standard at every stage of production. Every new part undergoes a quality assurance inspection before every operation.
For instance, after a flat blank is laser cut, it is immediately checked by our QC team. The same checks are applied after metal spinning the flat blank, trimming, 3D laser cutting, and any other processes that may be applied. This diligent process guarantees that every part meets the customer’s and our exacting standards before it leaves our facility.
Finally, before a part is shipped to the customer, it undergoes one last comprehensive check, ensuring that what reaches our customer is nothing short of perfection.
Guide
How Does Pricing Work?
Generally, the pricing process stays the same as it would for the first group, but of course, there is the difference between rolling and spinning.
Rolling will get a seam-weld step (most of the time) to join the two ends of the rolled blank together—with this being two steps, it will add onto the pricing. Instead of rolling, metal spinning is usually just one process—note that most of the time, spun metal will get a trim step, whether it’s trimming in a cell or on our 5-axis laser, which is another process.
However, metal spinning, most often, requires high tooling costs which may not be the most cost-effective route. To add onto the costs, metal spinning usually starts with circular flat blanks which take up more space per sheet than a rectangular flat blank for rolling will.
Let’s take our stainless steel funnel for example.
The estimators will conclude that the best approach to making a funnel will be to cut a flat blank on our laser cutter, spin the metal into shape, and trim it. For factors that most influence the cost, the estimators will look at using
stainless steel instead of mild steel for better environmental protection, using the appropriate thickness, and reducing operations wherever possible to reduce the quoted price for the customer.
Wrapping Up
Let’s shape the future together!
If you’re interested in learning more about our services, wanting a deeper understanding of our capabilities, or simply obtaining a quote for your project, don’t hesitate to contact our KRYTON team. We’re always ready to turn your ideas into reality with our state-of-the-art metal spinning techniques.