Lorem ipsum dolor sit amet, consectetur adipiscing elit, sed do eiusmod tempor incididtat non proident.
Made in the USA since 1981.
Metal Spinning delivers high-performance, expertly crafted parts that meet your exact specifications.
Also called spin forming, metal spinning shapes metal into axially symmetric parts by rotating a flat blank on a lathe and applying the right amount of pressure. The result is the exact piece you need—a precise, durable shape that completes your project.
Why Metal Spinning Works for Your Project
Metal Spinning produces high-quality parts quickly and without breaking the budget. This metalworking process offers:
Flexibility in Design
Adjust your product design on the fly. Metal spinning allows for evolving designs without extensive retooling.
Superior Strength and Finish
Metal spinning ensures smooth, durable components that are both strong and aesthetically pleasing.
Cost-Effective Tooling
Metal spinning keeps costs low, with tooling typically only 10% of the price of methods like stamping or casting.
Fast Turnaround
Metal spinning beats your short lead time with tooling and parts ready within weeks, not months.
Ready to learn more? Connect with us and let’s discuss your needs.
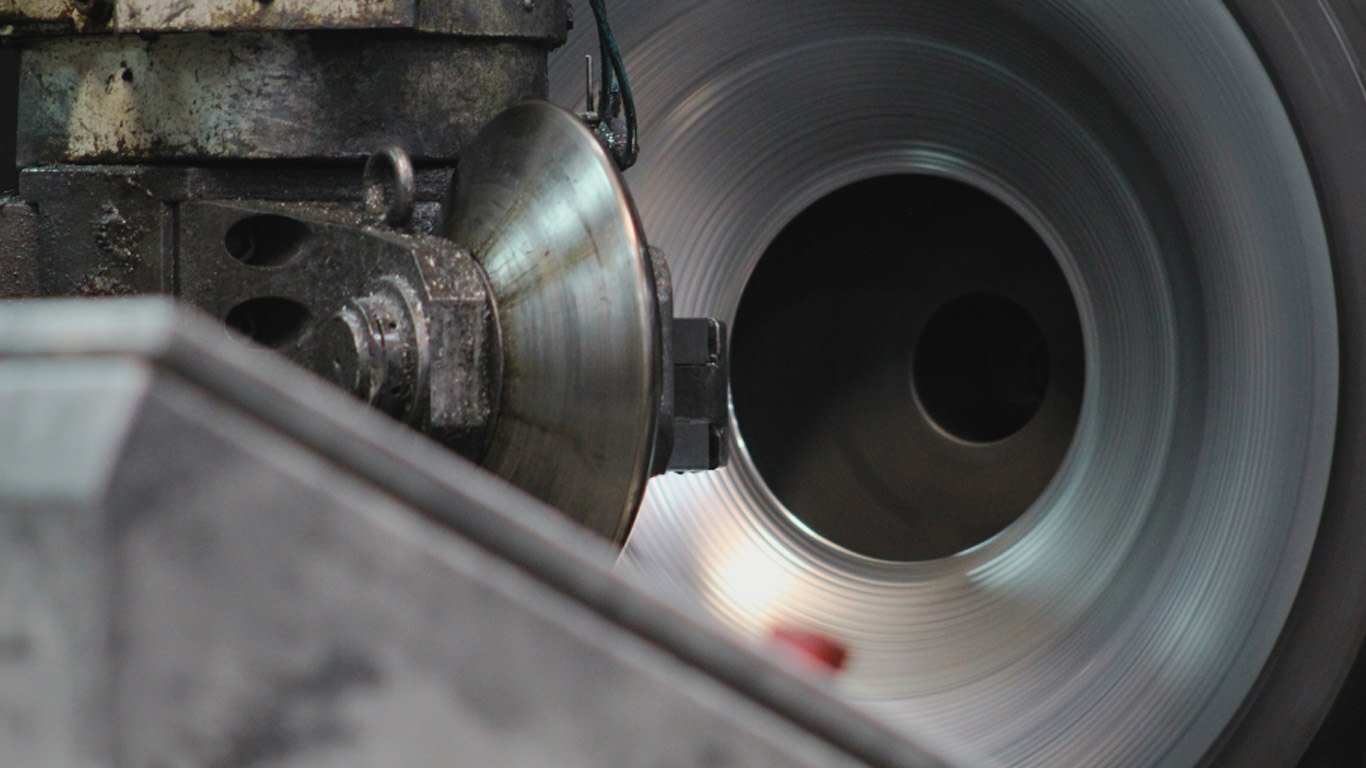
Our Capabilities Geared For You
Your project exists on its own timeline, with a set of requirements that are unique to the task at hand. Here’s what KRYTON brings to your metal mission:
Automatic CNC Spinning
Achieves flawless, high-volume production with unmatched precision and efficiency.
Hydraulic-Assist Spinning
Handles medium to large-scale tasks with the perfect balance of power and detail.
Manual Hand Spinning
Crafts custom, intricate parts with exceptional attention to detail and craftsmanship.
Our process enables us to handle parts up to 60 inches in height and 100 inches in diameter. Whether you need a single prototype or a high-volume production run, we are equipped to meet your required quantities.
Metal Specs You Can Count On
We work with a variety of materials and different levels of thickness:
- Brass: 0.030” to 0.187”
- Stainless Steel: 0.030” to 0.187”
- Carbon Steel: 0.030" to 0.375"
- Aluminum: 0.025” to 0.500”
- Copper: 0.022” to 0.125”
combine with 5-axis laser cutting
Our 5-axis laser cutting technology adds versatility to metal spun parts, allowing us to cut precise holes, slots, and cutouts on curved surfaces. This capability means complicated features can be added to spun components—adding cost-effective value with less effort.
Industries We Serve
Supporting your industry with reliable, high-quality solutions.
- Agriculture
- Air Movement & Ventilation
- Emergency & Signal
- Energy
- Food
- Medical & Scientific
Lorem Ipsum
Lorem Ipsum
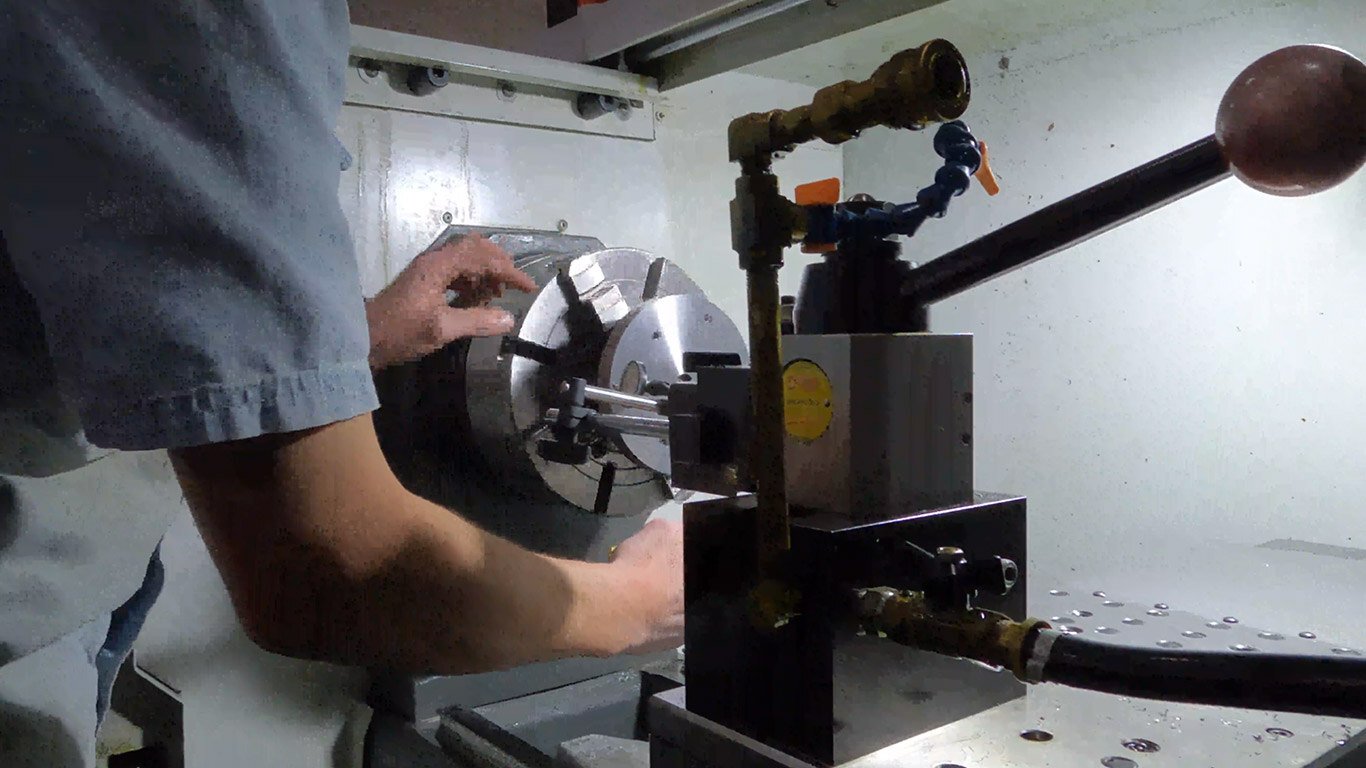
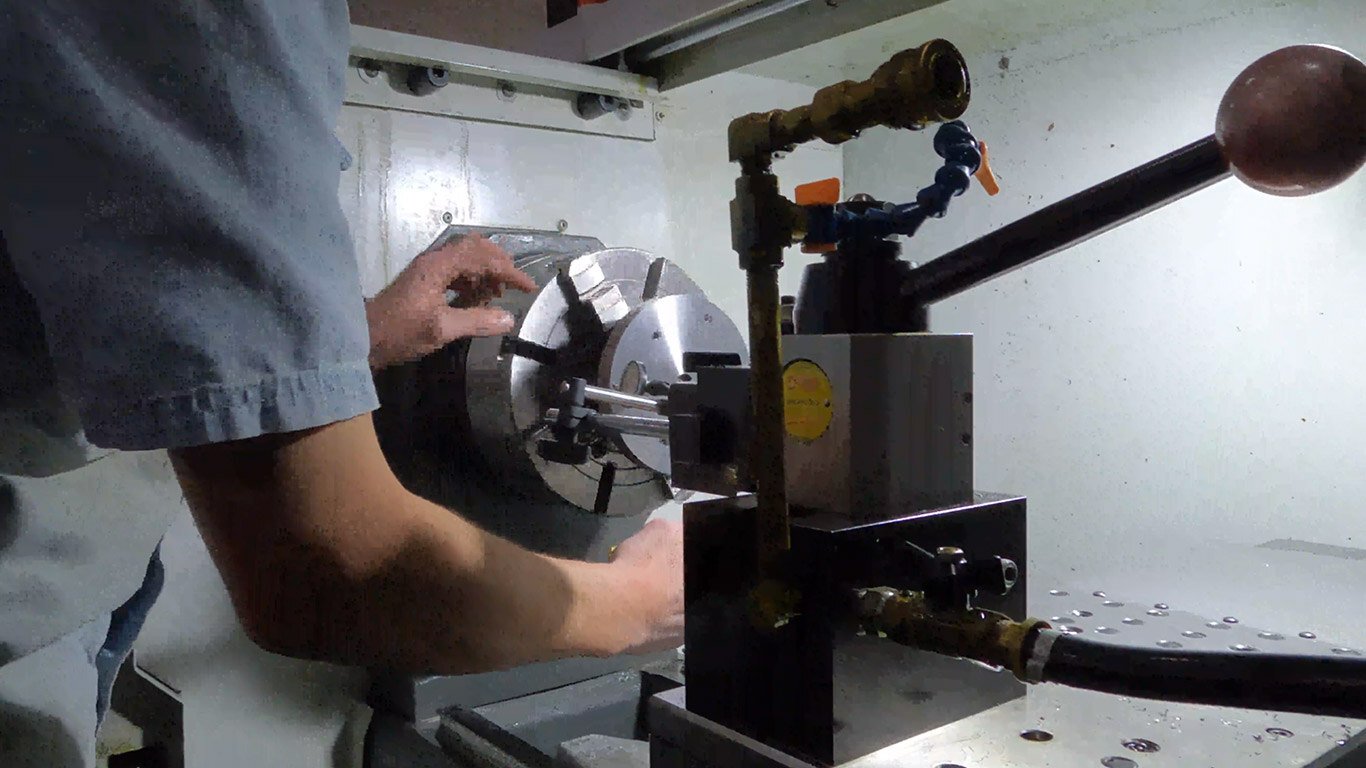
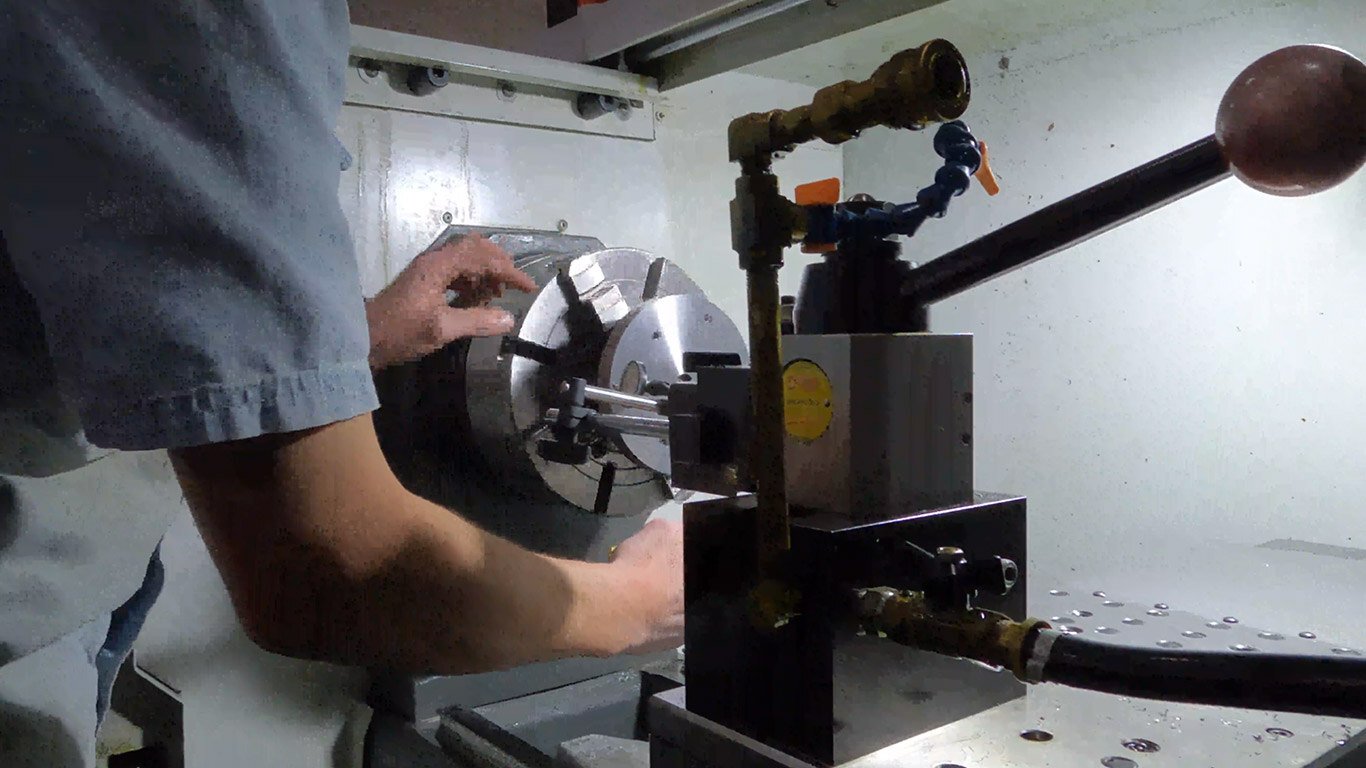
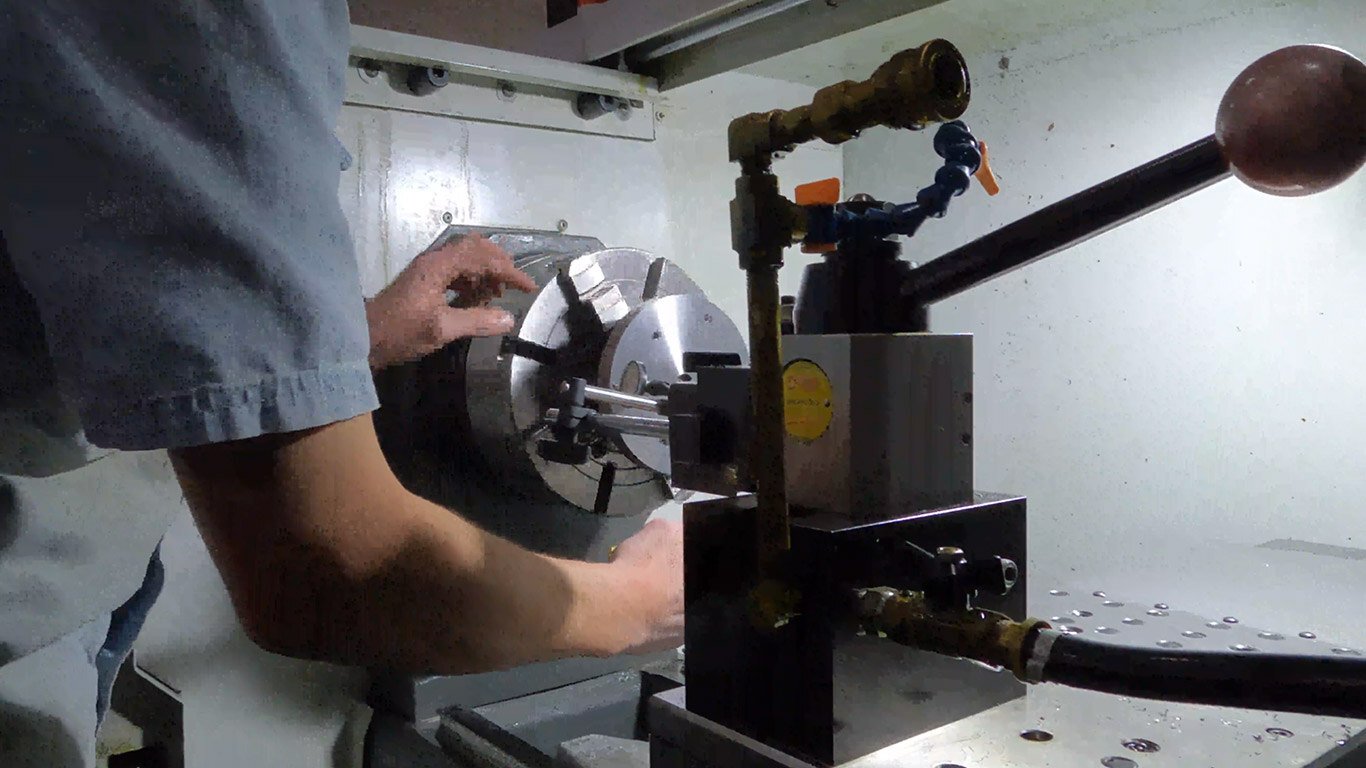
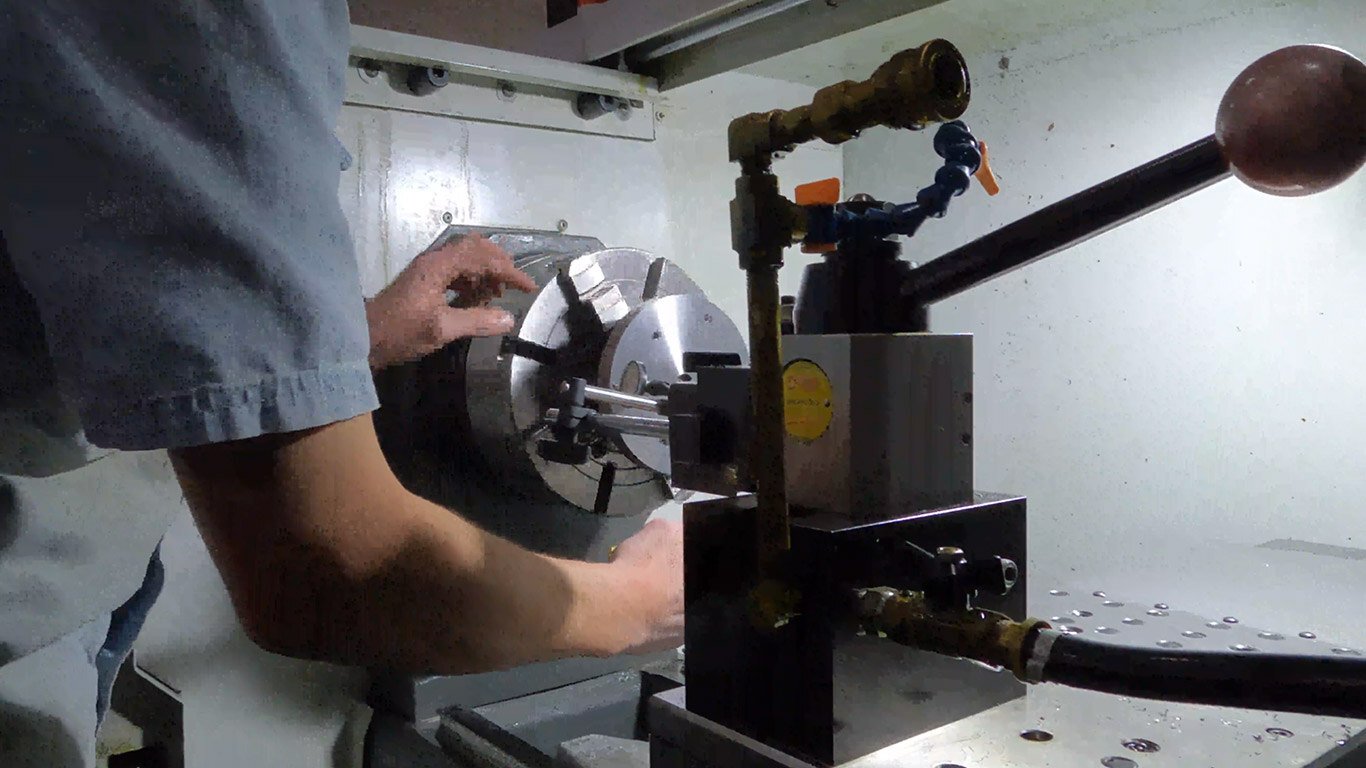
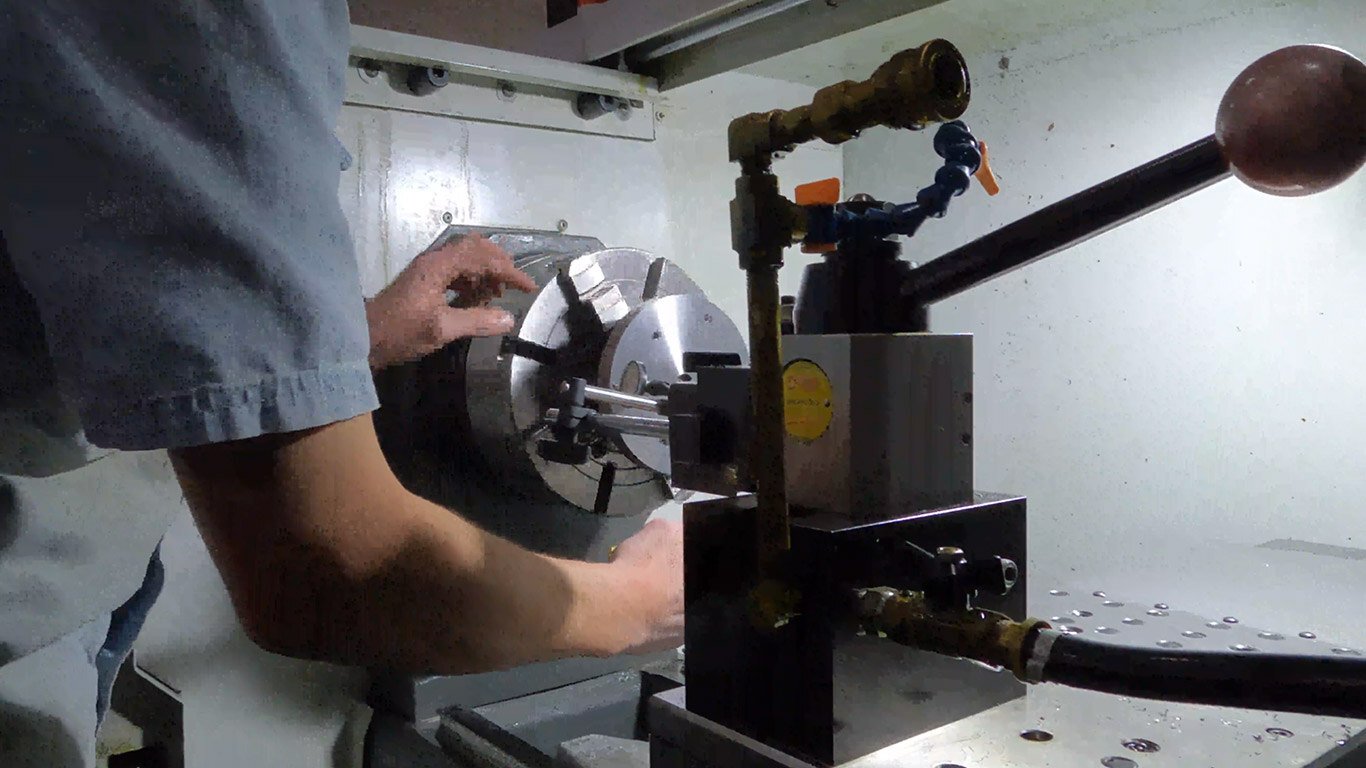
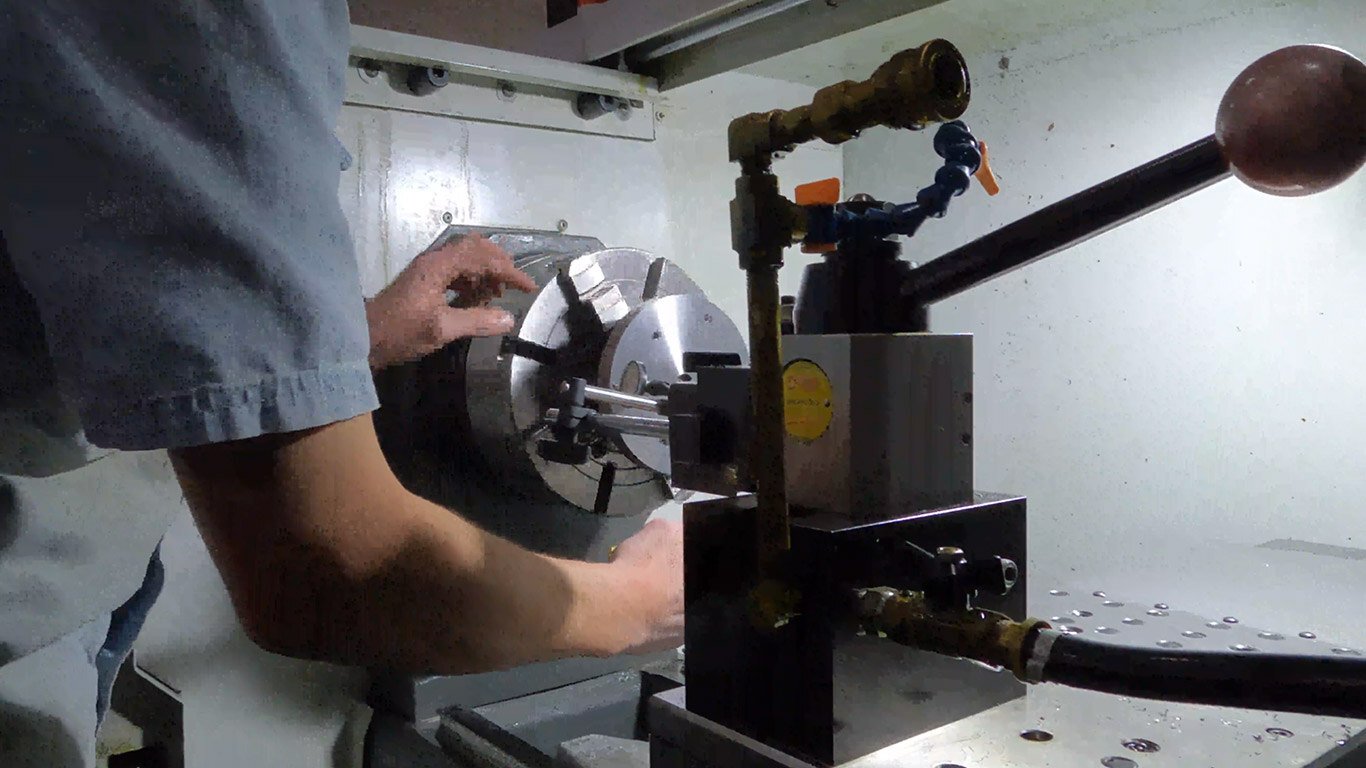
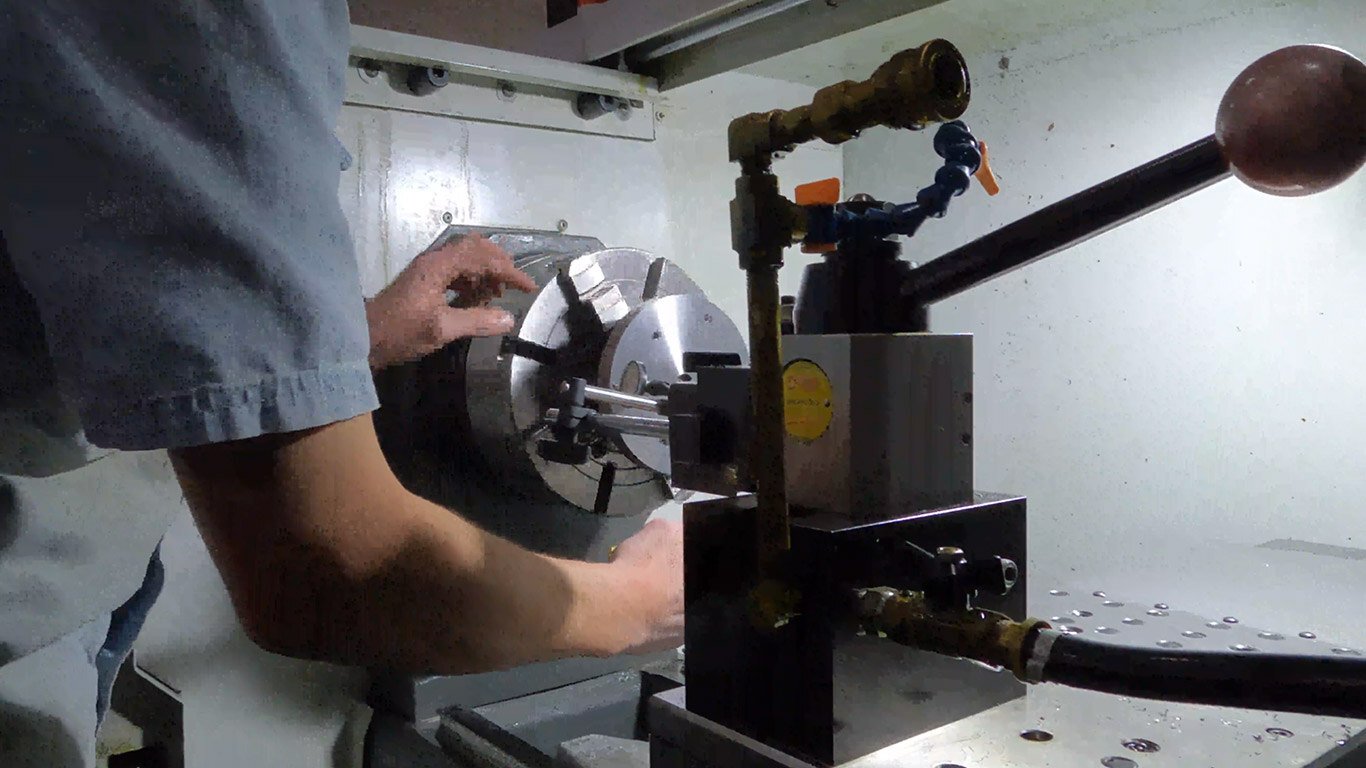
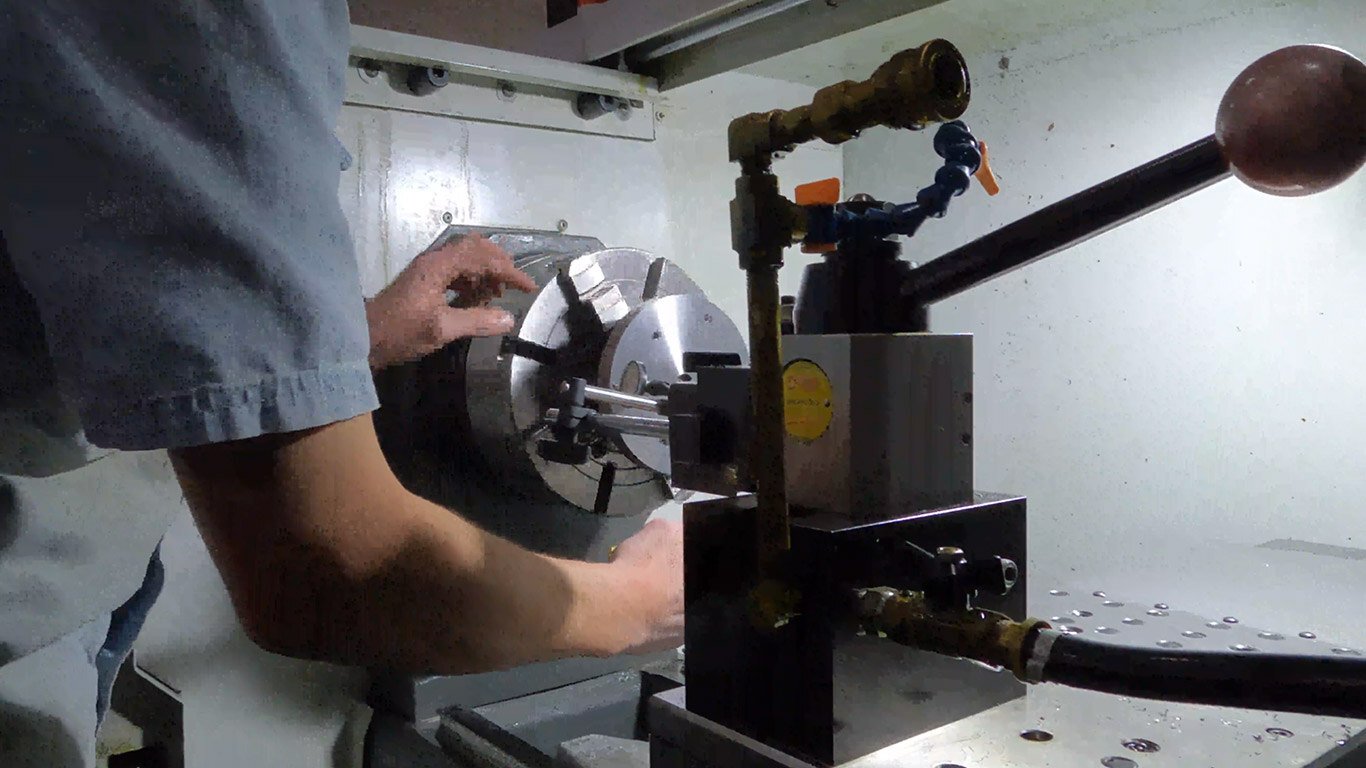
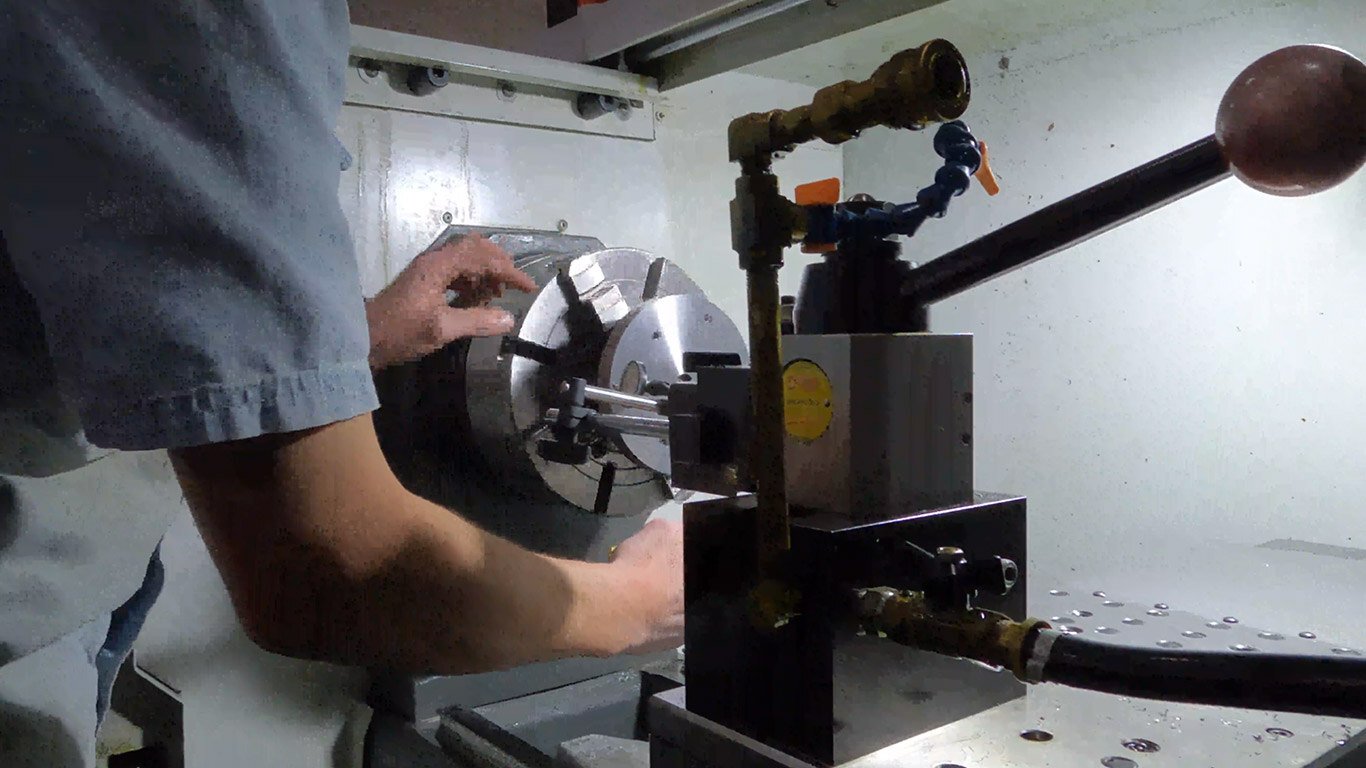
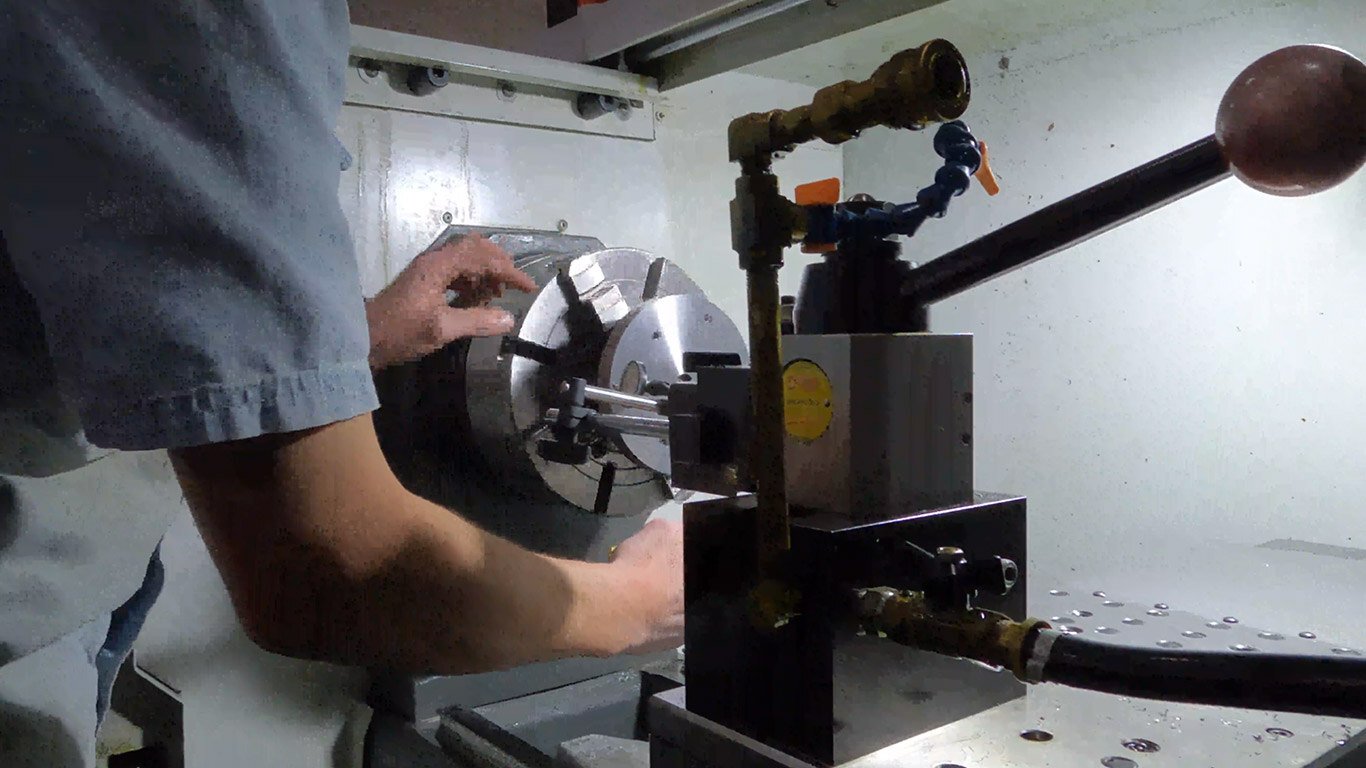
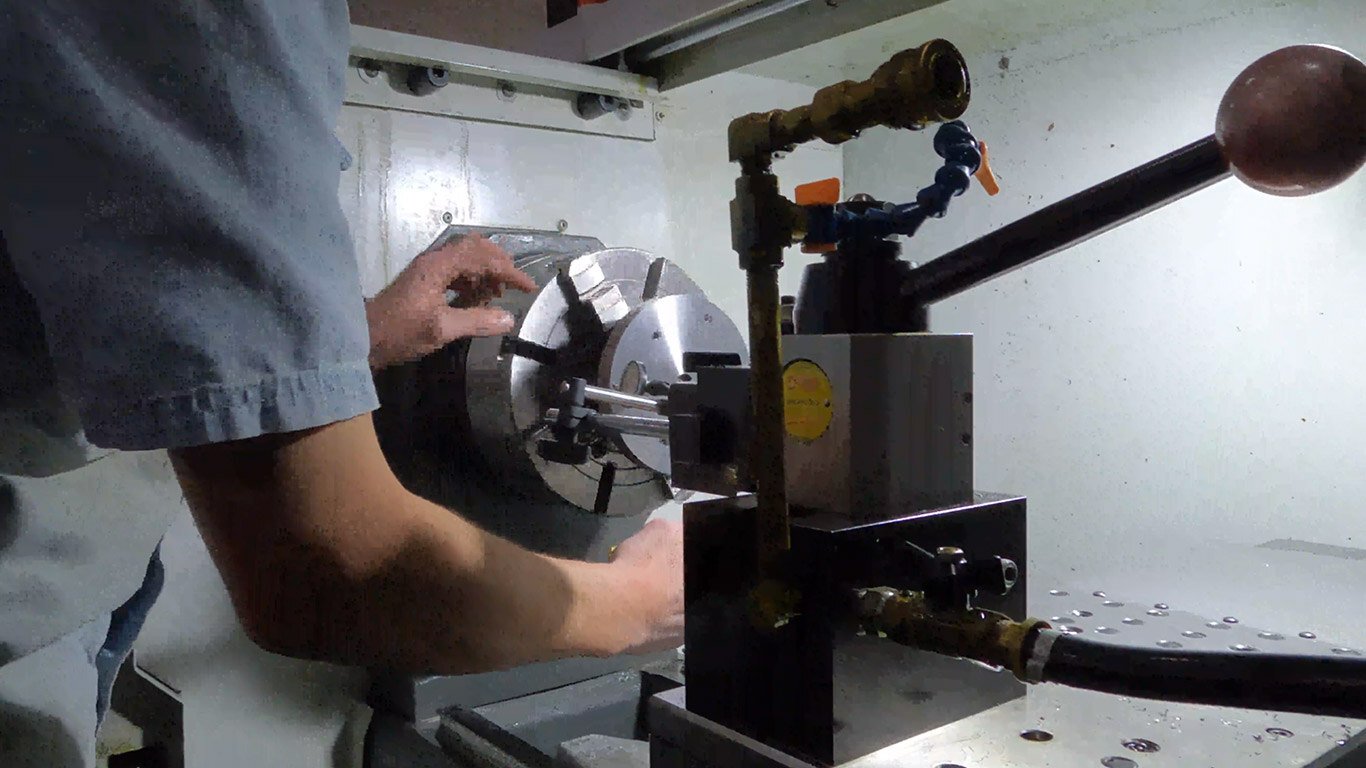
Ready to learn more? Connect with us and let’s discuss your needs.
Metal Spinning FAQs
What is metal spinning?
Metal spinning is a metalworking process that uses a lathe to rotate a metal disc or tube and shape it into an axially symmetric part by applying localized pressure. This method is used to produce a variety of shapes, including cones, cylinders, and hemispheres, without welding or seams.
What materials can be spun?
A broad range of materials can undergo the metal spinning process:
- Aluminum: Lightweight and corrosion-resistant, ideal for automotive and aerospace applications.
- Brass and Copper: Excellent for decorative and conductive parts.
- Stainless Steel and Carbon Steel: Offers superior strength and durability, suitable for industrial applications.
- Specialty Alloys: Such as Inconel and Hastelloy, used in high-performance and high-temperature environments.
How does metal spinning compare to other forming processes?
Metal spinning is often more cost-effective and versatile than stamping or casting. It is ideal for producing symmetrical parts with smooth surfaces and can achieve tighter tolerances than some other methods. Additionally, it offers lower tooling costs and quicker lead times.
What shapes and sizes can be achieved?
Metal spinning can create a variety of shapes including:
- Conical: Tapered parts like funnels and cones.
- Cylindrical: Tubes and cylinders.
- Hemispherical: Domes and rounded parts.
We can handle parts up to 102 inches in diameter and possibly up to 0.50 inches in material thickness.
What tolerances can be achieved with metal spinning?
Tolerances for metal spinning can range from 0.015" to 0.250". Tighter tolerances can be achieved depending on the material and part specifications. We work closely with customers to meet specific tolerance requirements for their applications.
Can metal spinning be combined with other processes?
Yes, metal spinning can be integrated with other metal-forming processes such as:
- Hydroforming: For complex shapes.
- Machining: For precision details.
- Welding: For assembly of multi-part components.
What industries use metal spinning?
Our metal spinning services cater to a wide range of industries, including:
- Aerospace & Defense: Components like heat shields and combustion chambers.
- HVAC / Air movement: Components like reducers, fan panels, duct fittings.
- Agriculture: Cab parts, exhaust parts, and grain handling parts for equipment.
- Automotive: Parts like wheel rims and hubcaps.
- Food Processing: Equipment like kettles and fryers.
- Energy: Components for oil & gas, nuclear, and renewable energy sectors.
- Medical: Parts for MRI machines and other medical devices.
What are the lead times for metal spinning projects?
Lead times for metal spinning projects can vary based on the complexity and volume of the order. However, our efficient process typically allows for turnaround times ranging from a few weeks for small runs to several weeks for larger, more complex orders.
Do you offer prototyping services?
Yes, we offer prototyping services to help you develop and refine your designs before committing to full-scale production. Our prototyping capabilities ensure that your final product meets all specifications and performance criteria.
How do I start a project or get a quote?
Contact our team through our website or by phone. Provide details about your project, including material specifications, dimensions, and quantity.
Reach Out